Digital linking is an important element in securing competitiveness in medium-sized mechanical and plant engineering companies. Complex machines and plants are linked with industrial services, such as maintenance or digital remote services, in order to tailor individual customer solutions. Responding to customer needs through an economical combination of data-based services and physical on-site services requires cross-company value creation: In the sense of cooperative service provision, players such as machinery and equipment manufacturers, IT and service providers bundle their core competencies and create complex, innovative value networks. We have summarized the ten reasons for such co-production of industrial services:
1. new business models
The use of service modules from partner companies offers plant manufacturers and operators as well as maintenance service providers new opportunities in terms of hybrid services to secure customer benefits.
2. New value creation potential
By integrating the service modules of partners through an IT ecosystem, previously untapped value creation potential can be realized. For example, linking players from different specialist areas such as mechanical engineering and IT and services enables complex and innovative services to be created.
3. focus on the core business
The network of different players in co-production allows the company to focus on its own core competencies and at the same time to utilize the diverse core competencies of partners.
4. drive digitization
By joining a network for the co-production of industrial services, approaches to digitization automatically find their way into one’s own company. These are coordinated and further developed by experts over the course of the network partnership.
5. specifications for order processing
Standardized specifications ensure goal-oriented order processing. On the one hand, this ensures the co-production of industrial services, and on the other, it removes initial entry hurdles for new network partners and guarantees unproblematic integration into the network.
6. Access to new markets
The possibility of selling individual service modules in an ecosystem opens up new markets for network participants. New customers can be acquired.
7. service design standards
Overarching service design standards across companies enable a uniform and sustainable language for the development and implementation of further networked services.
8. sustainable corporate cooperation
A common, comprehensible order processing process of cooperating network partners promotes current and future cooperation and, as it were, new cooperations.
9. transparency of network partners
By bundling service providers and their services, machine and plant operators can select required services from a large portfolio and offer them to their customers. Service providers can also communicate their services in a user-oriented manner.
10. Enabling service engineering
Comprehensive tools and methods enable companies to develop, model and implement services independently.
Convinced? Then you too should start co-production and benefit from the numerous advantages to strengthen your competitiveness. In the spirit of #TogetherWeAreStrong, the current pandemic offers a good starting point to launch a collaboration.
Co-production of industrial services offers enormous potential, especially for German SMEs. However, until now there has been a lack of a uniform language that ensures efficient and secure linking of different companies at the network level. The BMBF-funded research project SealedServices (www.sealedservices.info) is therefore developing a cooperative value creation network with which Internet-based services can be realized independently by SMEs. The aim is to enable consistent and secure integration of data and services from different partner companies.
Experts and Contact Persons:
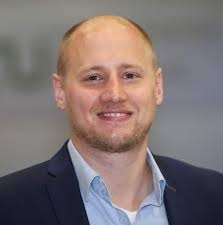
Lehrstuhl für Unternehmenslogistik LFO
TU Dortmund
austerjost@lfo.tu-dortmund.de
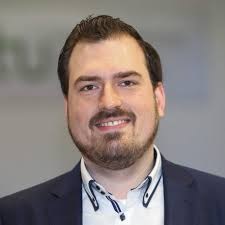
Lehrstuhl für Unternehmenslogistik LFO
TU Dortmund
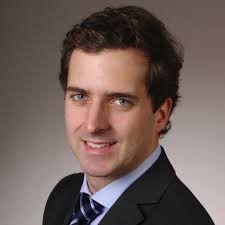
Fraunhofer-Institut für Materialfluss und Logistik IML