Energy and raw materials form the fundamental basis for the producing economy and for a consuming society. The competitiveness of manufacturing companies is closely linked to the availability and demand for energy and raw materials. Decreasing reserves of fossil fuels, a globally rising energy demand and an equally strong increase in global demand for fossil and renewable raw materials are increasingly presenting companies with economic challenges.
In recent years, companies have begun to rethink and ecological goals have been anchored in corporate strategies. Companies are not only concerned with the energy efficiency of the goods to be produced, but also with the energy efficiency potential of their value-adding activities in production and logistics.
Today, we have listed the ten potentials and challenges of considering energy efficiency as a planning target in the design of production and logistics networks.
- Early Planning Holds High Savings Potential
Consider the topic of energy efficiency already during the design or planning of a redesign of value networks. For example, the choice of location, volume allocation, the selection of supply strategies and the definition of transport modes have a decisive influence on your energy efficiency. This is where the key parameters with the greatest impact on energy efficiency can be influenced.
- Energy Efficiency – a Strategic Issue
At which costs and how energy-efficiently a product can be produced and transported in the network depends on the quality of your planning, the consideration of the essential parameters and their integration into the strategic and tactical network planning. If energy efficiency becomes an essential and strategic goal and is planned in detail accordingly, costs can be saved.
- New Target Figure
In addition to the classic performance and cost parameters, your company should take energy efficiency into account as a further target parameter. For this purpose, employees must be trained accordingly.
- Evaluation of Energy Efficiency
Once the decision for an energy-efficient design of your production and logistics network has been made, you are often faced with the question of which methods and concepts are now appropriate for evaluating energy efficiency. There are approaches that are unsuitable for practical use, but some of them are very complex. It is a good idea to enter into an exchange with research and together find the ideal way for your company.
- Cross-Company
Energy efficiency is an overarching theme and should be considered throughout the entire planning process, across all planning levels, down to the shop floor. Dissolve classic departmental thinking. This will support your company in the integrated planning process and promote a process orientation.
- Low Prioritisation of Energy Efficiency by Companies
Often the issue of sustainability and energy efficiency is considered of secondary importance. Classic economic aspects such as sales, revenues, costs, performance, etc. are usually at the forefront when planning and designing production networks. Energy saving potentials are only taken into account if they have a significant impact on costs. This fact makes an energy-efficient approach across the entire network difficult. Someone has to make the start. Set a good example – for the benefit of our society.
- Improving the Corporate Image
Sustainability awareness has increased in recent years, both overall and among your customers. The consideration of energy aspects promotes your corporate image, strengthens your social responsibility and thus customer loyalty.
- Lack of Transparency in Supply Chains
Energy efficiency does not stop at the front door. Even better is to take a cross-network approach. The lack of transparency in the supply chain will present you with a challenge. Most companies know their direct suppliers, but when it comes to upstream suppliers, i.e. the suppliers before their own suppliers, the information situation is quite different. This is where the approach of comprehensive networking, i.e. digitization across the entire value chain, will provide medium-term support.
9 . Insufficient Data Basis
There is often no data available or only data of poor quality for the upstream suppliers. This effect is all the more serious the further back the value chain goes. This circumstance makes it more difficult to evaluate energy-specific aspects and to design an energy-efficient value-added chain. New tracking procedures or even smart contracts can be used to reduce
- Intransparency in the Product Composition
One challenge remains for the time being: If you do not know all suppliers, it will also be difficult to trace the composition of the product. Although every company gives clear specifications regarding the parts it supplies, these specifications do not cover the material composition. As a result, your company is often not able to see which materials have been used in the manufacturing process and, most importantly, where these materials come from.
Our Experts:
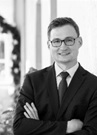
Fraunhofer Institute for Material Flow and Logistics
andreas.guenter@iml.fraunhofer.de

Fraunhofer Institute for Material Flow and Logistics
lea.vliegen@iml.fraunhofer.de